October 25th, 2018. 7h47.
I have just locked my bicycle to a “no parking here” pole located in an industrial area just outside Boston and make my way towards the Somerville United Parcel Services (UPS) sorting facility. Dr. Matthias Winkenbach and I are about to embark on a half-day delivery tour around Somerville and Cambridge Massachusetts, respectively. What follows is a not-so-detailed account of my observations and insight into the present and future of urban last mile delivery. Throughout this photo-documentary, we will try to answer a few questions, namely: what is last mile delivery? how does it work? and why should you care?
So, with no further ado, let us dive into this UPS story.
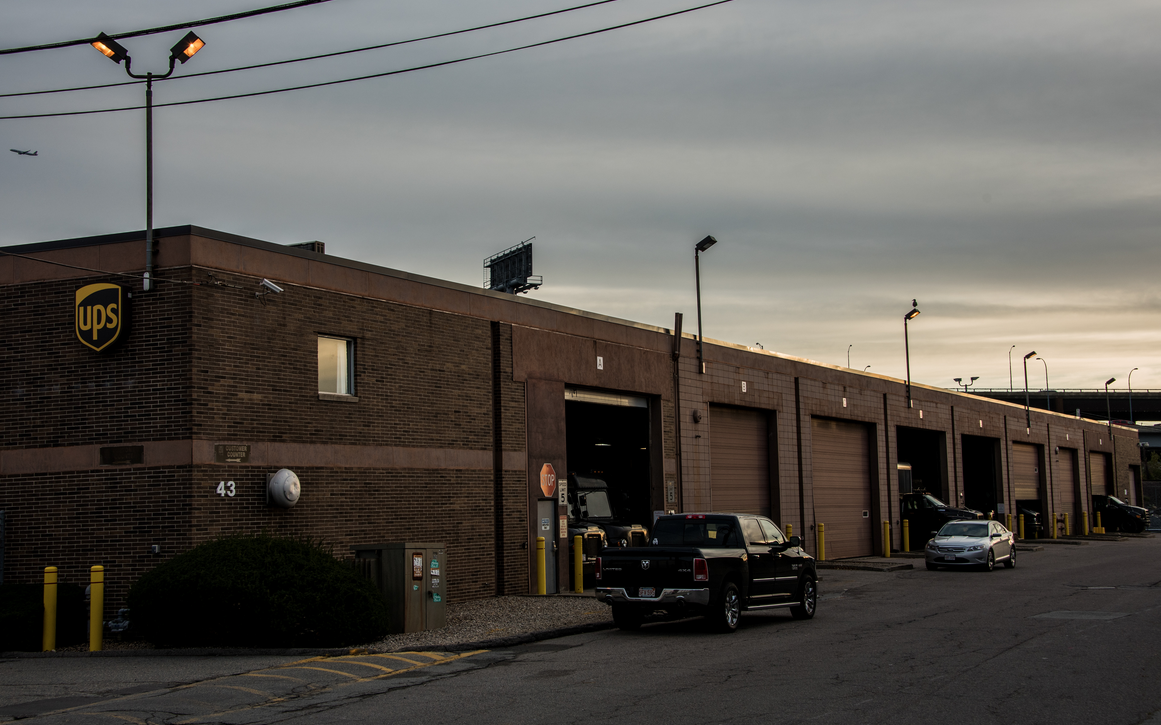
After having successfully passed the guard and metal detector that lead to the sorting area (in complete legality obviously), I joined Matthias in the break room on the office side of the building. We could hear the sorting happening bellow us: since the early morning sorters had been hard at work performing a process called cross-docking. In sorting facilities, or distribution centers (DC) as we also like to call them, packages arrive in large quantities and on large vehicles (trains, semis, etc.) from across country. Since each of these large trucks may contain goods that are destined to customers in very different areas and hard to access with large vehicles, each truck is emptied and each package dispatched to other, often smaller, vehicles. Thus, the packages go from one dock to another, often crossing each others’ paths.
After dressing up in our brand-new UPS uniform, Matthias and I were paired with two drivers. I was paired with John (whose name has been changed for confidentiality purposes). He in his 30s, rocking the long hair, and drinking a large Dunkin’ Donuts Latte. “Do you want to come do some exercise?” he asks me. John takes off and I follow in a rush to see what is going on. We enter a small room ‘decorated’ with performance indicators and metrics on the wall and grab a piece of cord and a pedal from the cart in the middle of the space. The thirty-something drivers, Matthias, and I stand in a circle. I take a quick glance at Matthias who is clearly struggling as much as I am at understanding what we have to do. I am still unsure to be honest. Anyhow, while we (well, the drivers) perform strengthening and stretching exercises (and we fail to copy), a manager gives an overview of the previous day’s performance. After ten minutes, the meeting is over, the string and pedals back in the cart, and the drivers hurry to their vehicles. It is now 8:53.
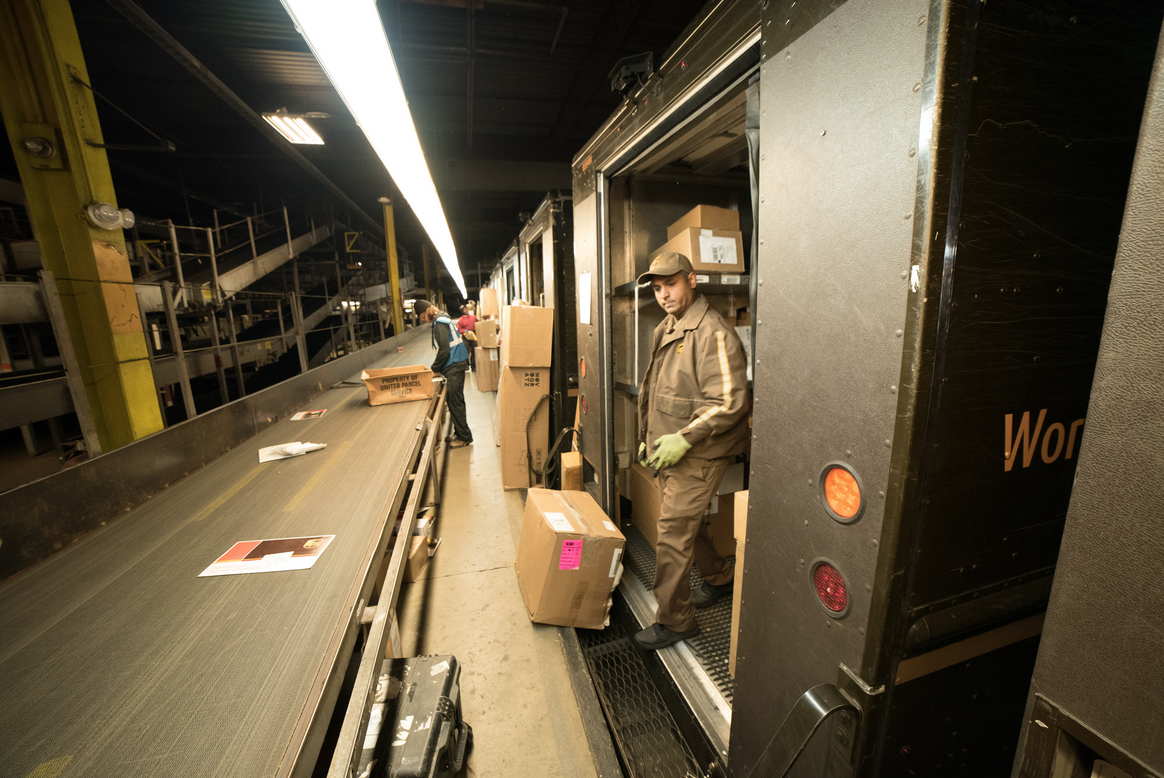
It is almost the end of the cross-docking exercise when we arrived at the van, but a few packages are still traveling on the belts that lead from the large trucks to the delivery vans (to the left of the picture above). The sorters are almost done filling the trucks up; each package should be placed on the shelves inside the van according to the map taped to the back of the vehicle (see picture below).
While John finishes placing the last few packages in the van himself he tells me that he has been working as a driver for UPS for about a year now and this is only the third time he takes this route. Because of his lack of seniority, John does not get his preferred routes; instead the route he is serving changes almost daily. As he places the last package inside he says, “but I don’t mind. It’s just that [finding the right place to deliver and park] takes a bit more time sometimes.”
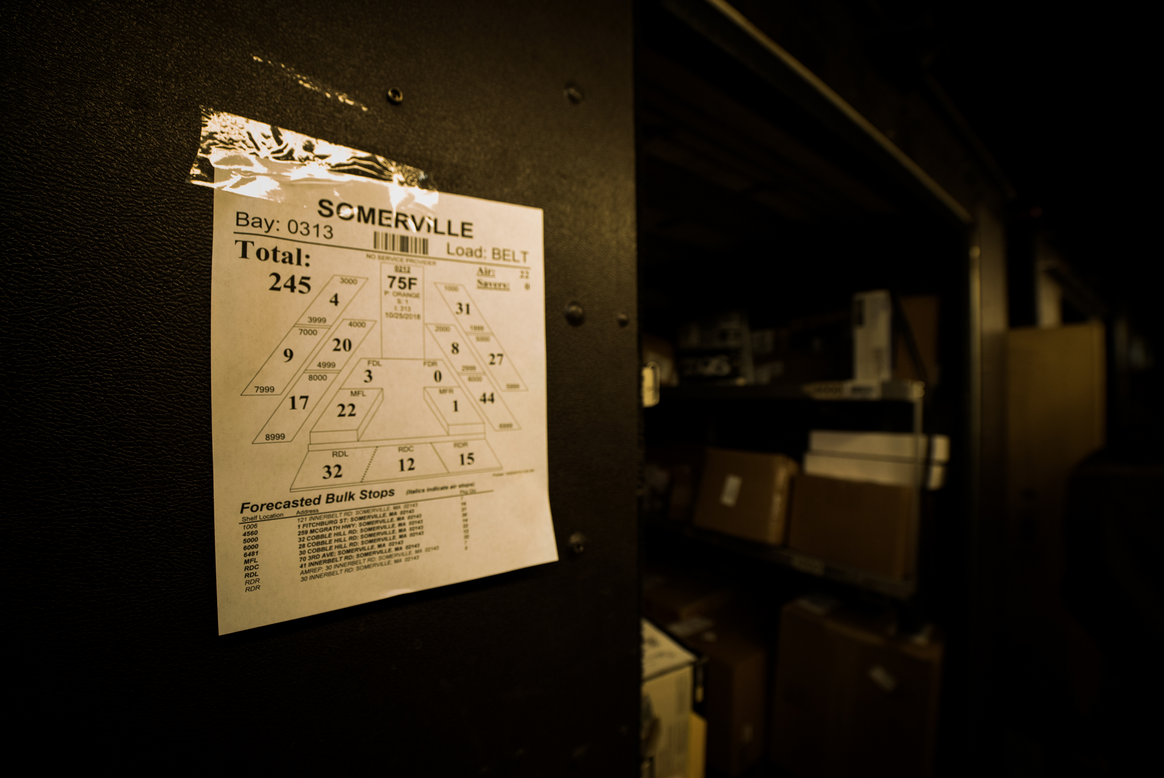
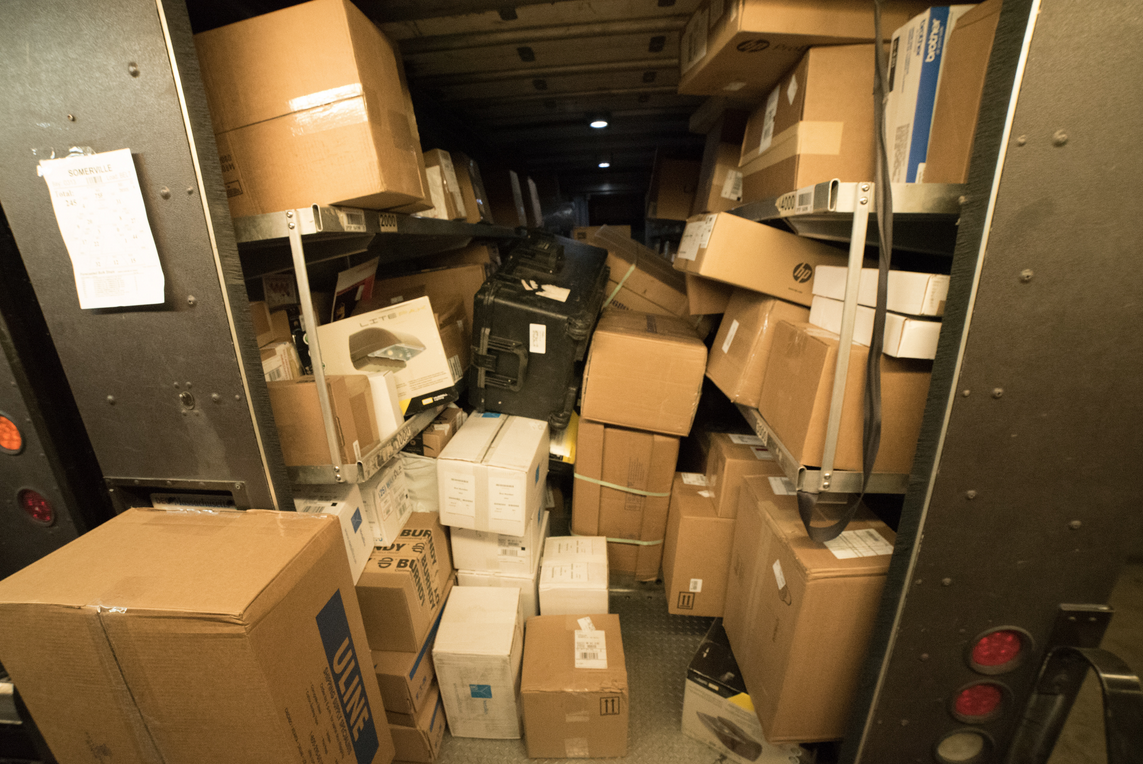
9:16. The van is almost fully packed. The alleyway is completely blocked: time to get going.
Many of the packages that John will be delivering today have been bought on the internet. The rise of e-commerce has drastically increased the number of packaged to be delivered. To give you an idea, in 2010 the United States Postal Service (USPS) delivered 3.1 billion packages. In 2017, 5.7 billion. This is close to a doubling of the volume and UPS, FedEx, and others have seen similar increases. It is good for business, but cities have had a hard time keeping up with problems caused by the added vehicles.
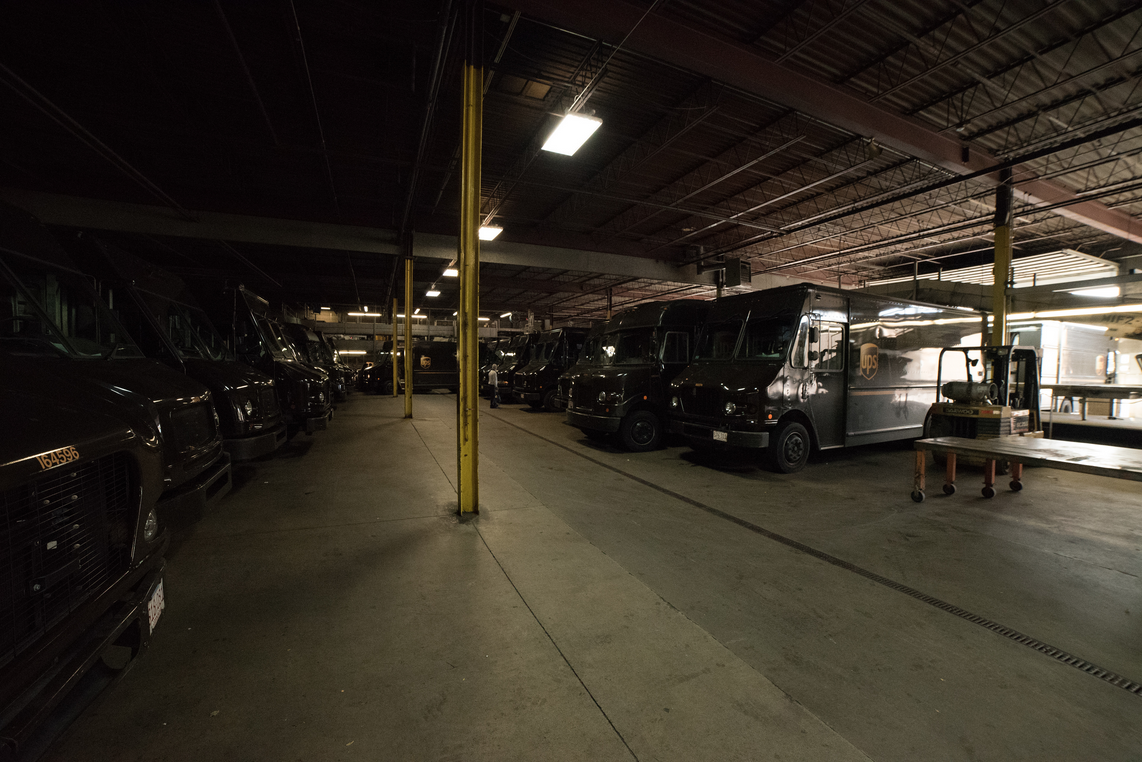
London actually imposed a congestion charge in 2003 (making vehicles pay to come into the city) that drastically improved traffic. A bit over a decade later, and after seeing congestion worsen, the city decided to see if the congestion charge still had its desired effect. Indeed, the change in number of vehicles entering the city everyday, as compared to before 2003, could not explain the worsened situation. It was found that the issue is instead the added number of vehicles navigating inside the city that is due, in part, to the rise of e-commerce and last mile delivery.
In the first quarter of 2018, e-commerce sales grew 14%. Concurrently, we, the end customers want our orders to arrive within a few hours, increasing the stress on the current system. This results in more vehicles on the roads, increases in congestion and pollution, and a degraded urban environment.
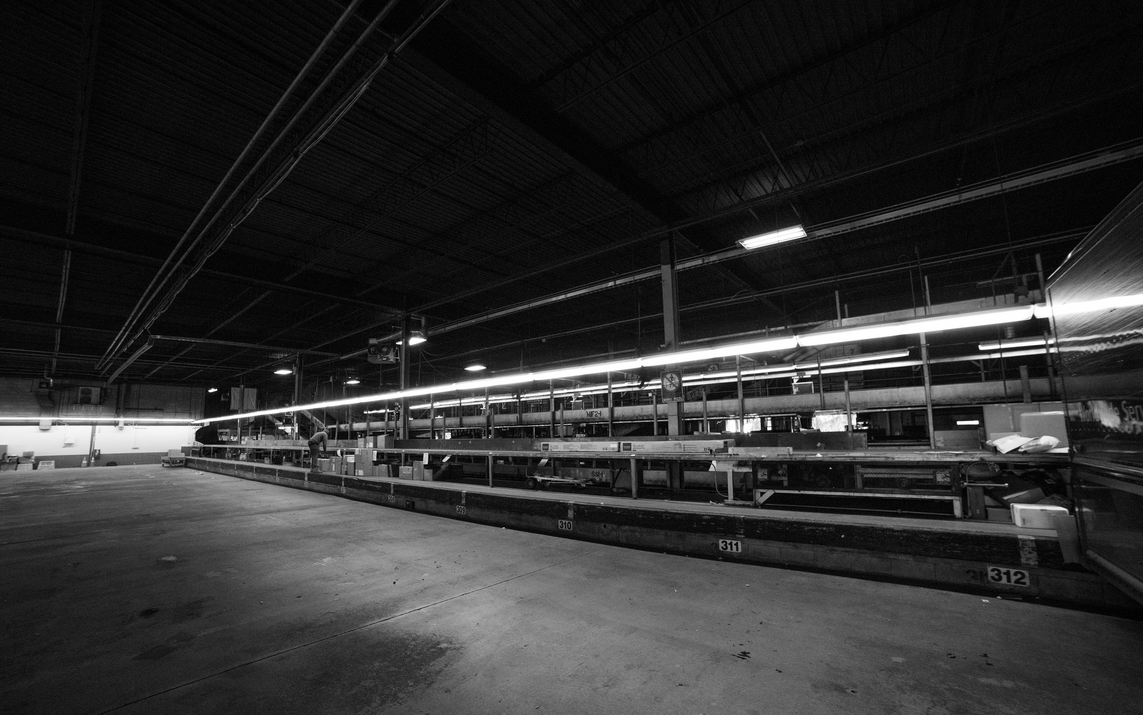
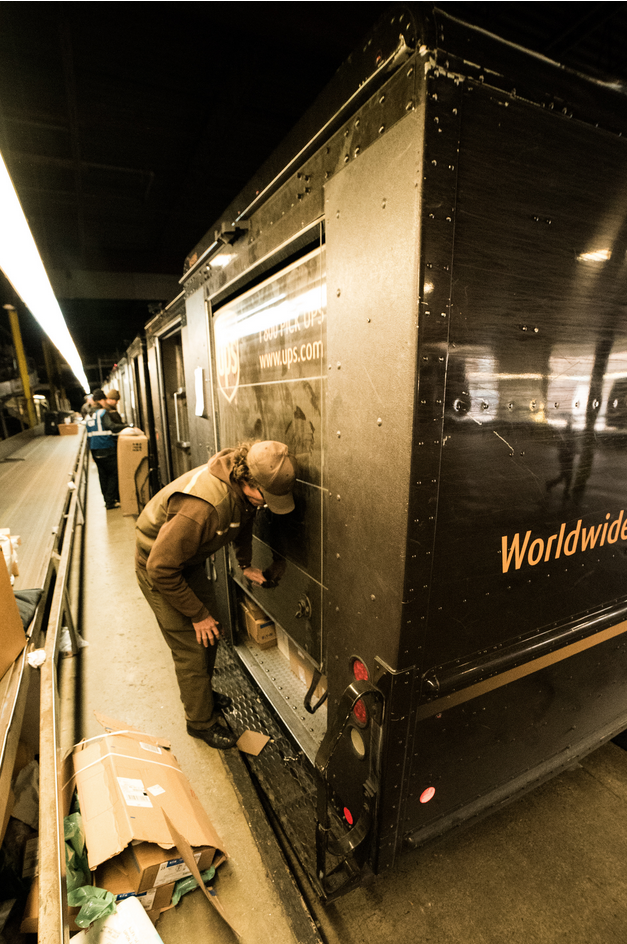
After a few failed attempts at closing the back of the van (the vehicle is absolutely packed), John is able to close the door and and we are ready to go. He sits in the driver seat and checks his DIAD (Delivery Information Acquisition Device) for the stops to be taken during the day. First introduced in 1991, the DIAD holds the delivery information for each package in the truck. It is used to scan bar codes on packages and for customers to sign off, and tells the driver the best route to take.
To be honest, the DIAD looks somewhat archaic: its black and white touchscreen is far from aesthetically pleasing and the user interface could probably use a few UX (user experience) consultants. But the DIAD does it’s job. John checks the order of the stops and tells me he will not follow them to the letter. He needs to go deliver the stops with most packages as soon as possible. This will allow him to remove some of the clutter in the back of the van and make it easier to find further packages. He puts the device down, and we head out.
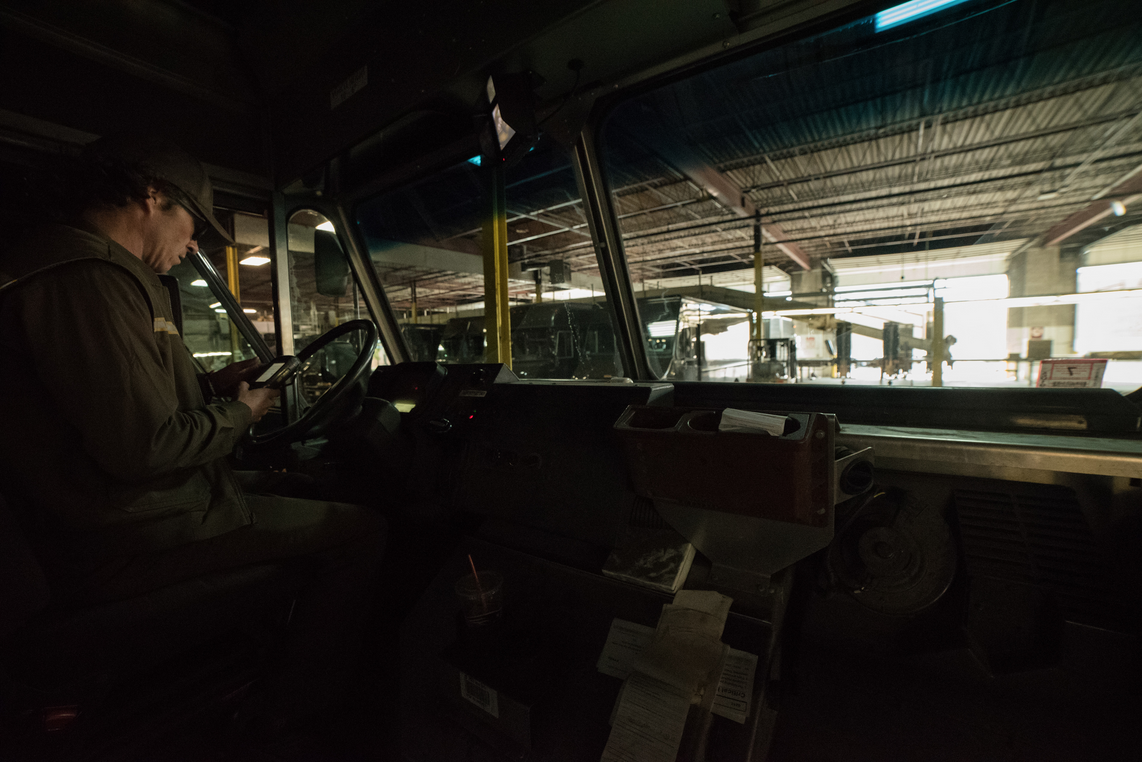
We reach our first stop, an electricity firm. I follow John inside as we go straight to the truck bay and open it up. John swings the back of the van open and speedily pulls out his DIAD to start scanning packages. The DIAD goes “bidup”: this package is indeed for this stop, “bidup”: here is another one, “bidow” this one does not belong to the current stop. There are 35 packages to be delivered here, most of which John finds within a few minutes. The last four are nowhere to be see. After a few minutes searching in vain, John decides to leave this stop: “we have some priority packages that need to be delivered before 10:30. I can’t waist more time searching for low priority packages. We’ll have to come back later.”
Since the last mile represents some 30% of the total costs of delivery and that, for many companies, shaving off a couple percent here or there could translate to millions in annual savings, urban last mile delivery optimization has become booming field. At the Megacities Logitics Lab (MLL) at MIT, and under Matthias’ supervision, we tackle some of the issues that changing customer behavior and expectation are bringing to the forefront. The MLL is primarily focused on the data-driven technology aspect of these solutions, where working with the existing infrastructure and legislation is key. This UPS journey inscribes itself in this quest for understanding how to improve the urban last mile while working around the current infrastructure in a minimally invasive way.
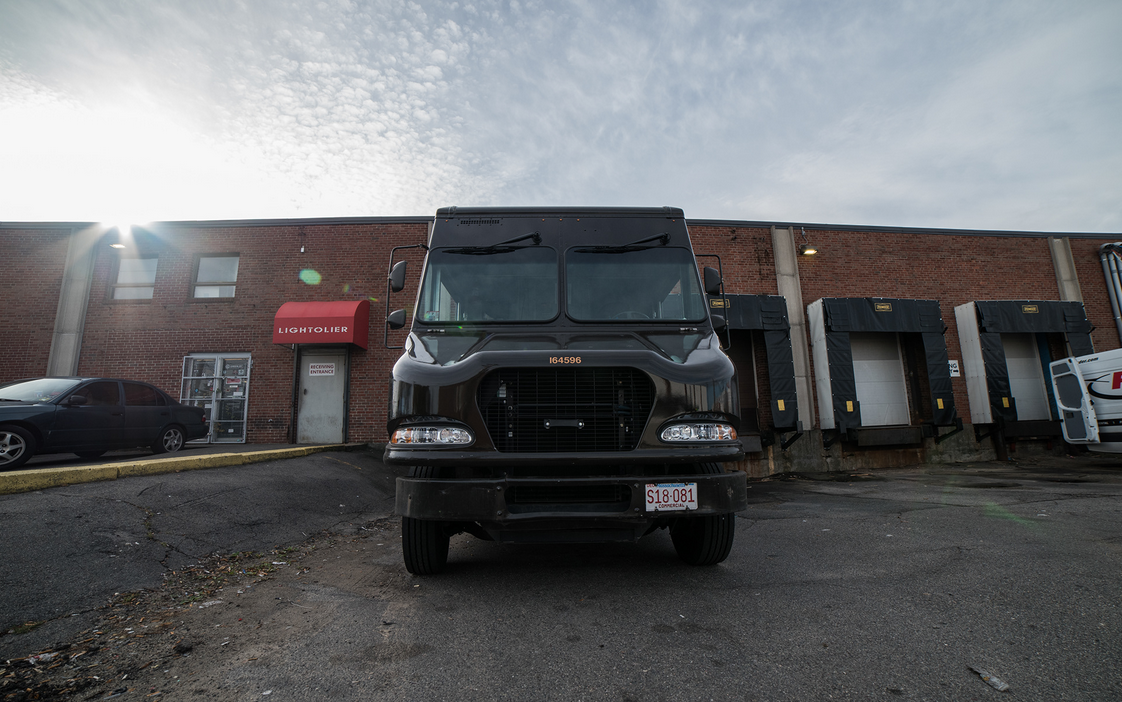
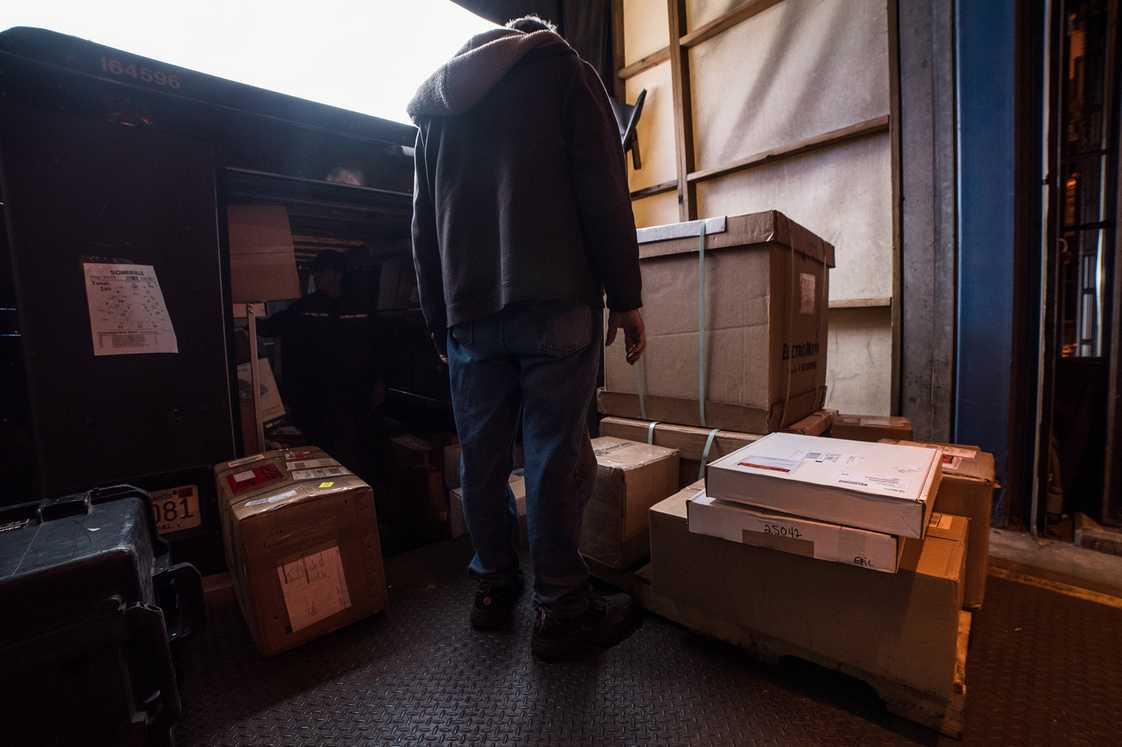
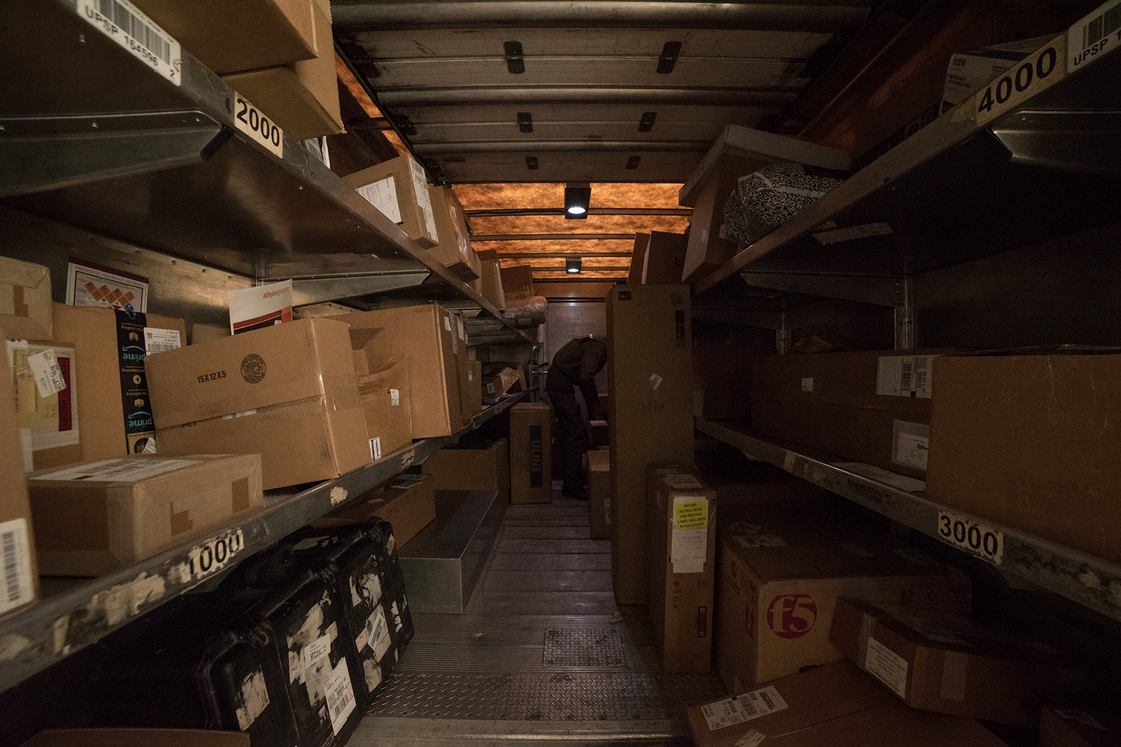
9:59. A few stops later and the truck is already half empty. John is looking for a missing package and again decides to come back later. He now has 31 minutes to make all five 10:30 deliveries left. I can feel that he is starting to be slightly stressed but that he knows he can do it, it just “depends on the traffic on main street.”
There is a repeating pattern this morning. John serves a stop; he cannot find one or more of the packages; he does not have enough time to continue looking; and thus, he will have to come back later in the day
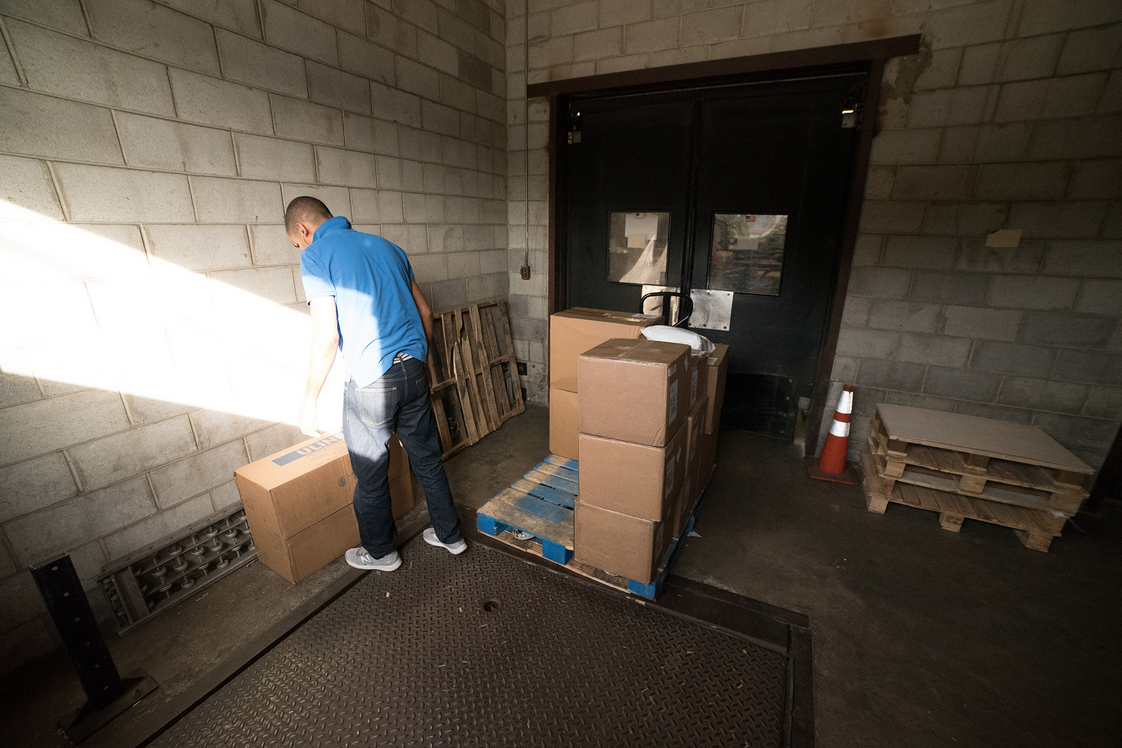
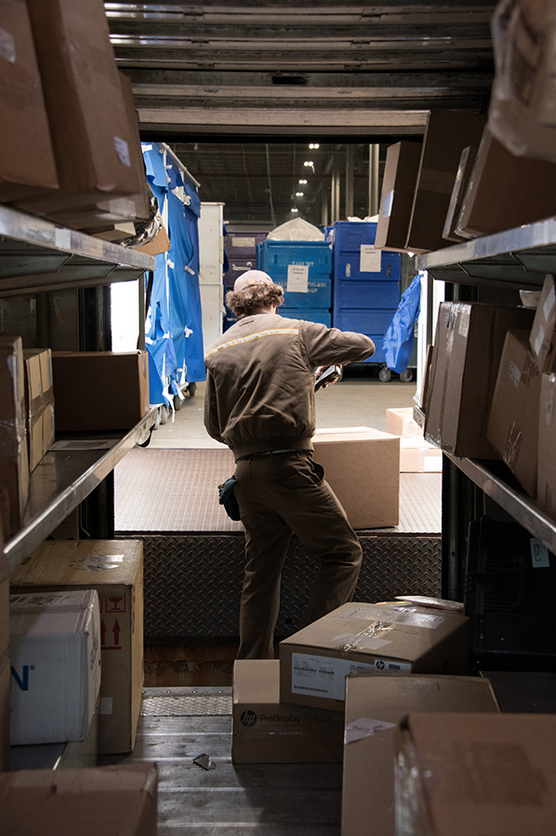
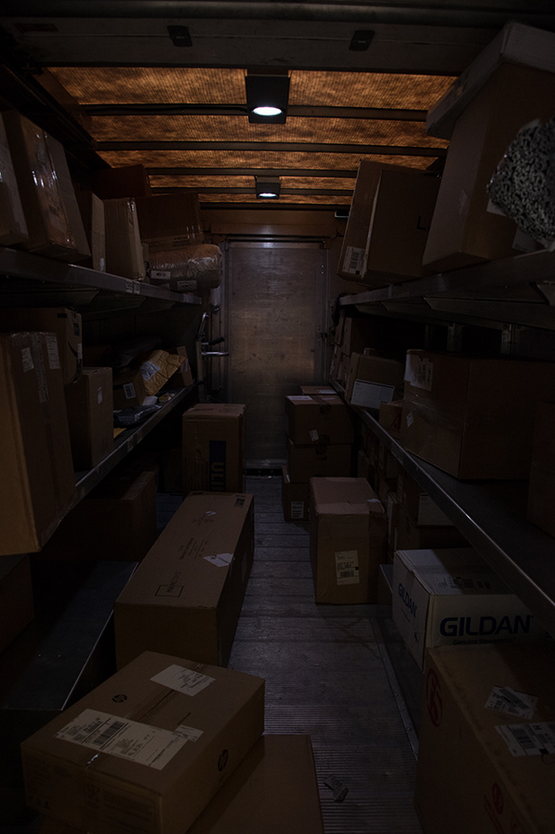
10:28. John parks the truck on a residential street, the last two 10:30 stops are here. I take one of the letters, he takes a few packages, we part ways. I place the letter on the porch. 10:31. Done. We walk back towards the truck. I can feel that the atmosphere is lighter; we get back in the van with a smile and continue the route.
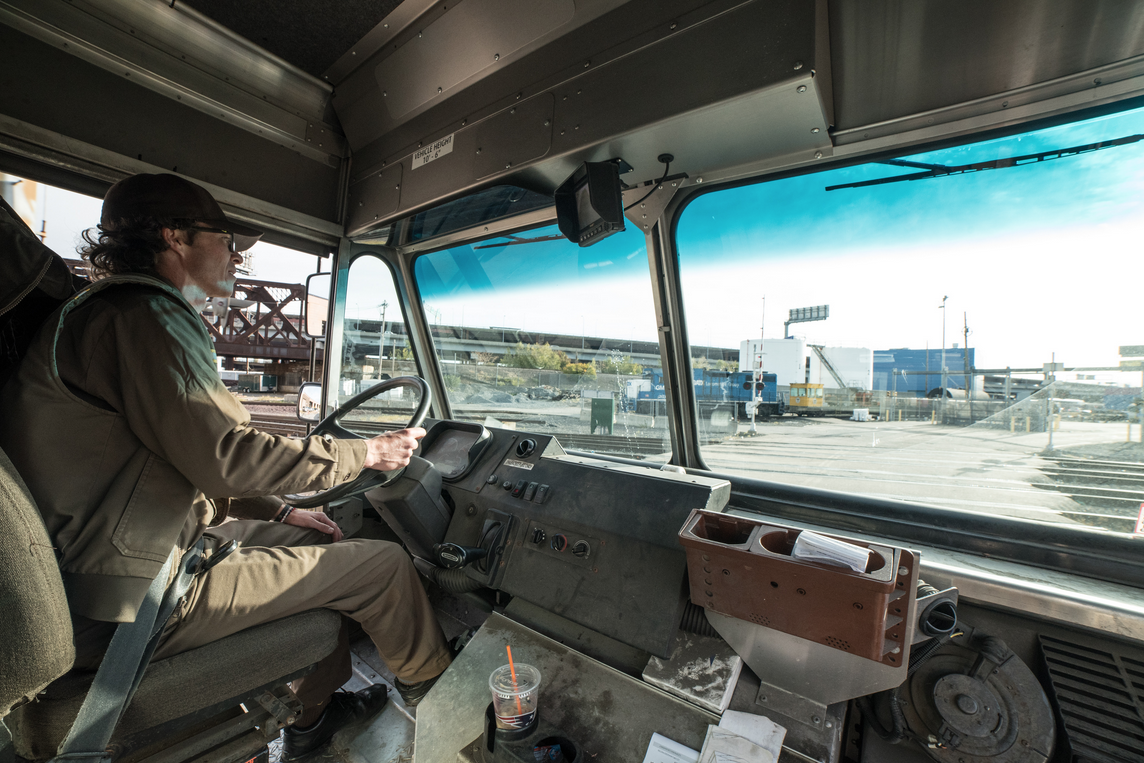
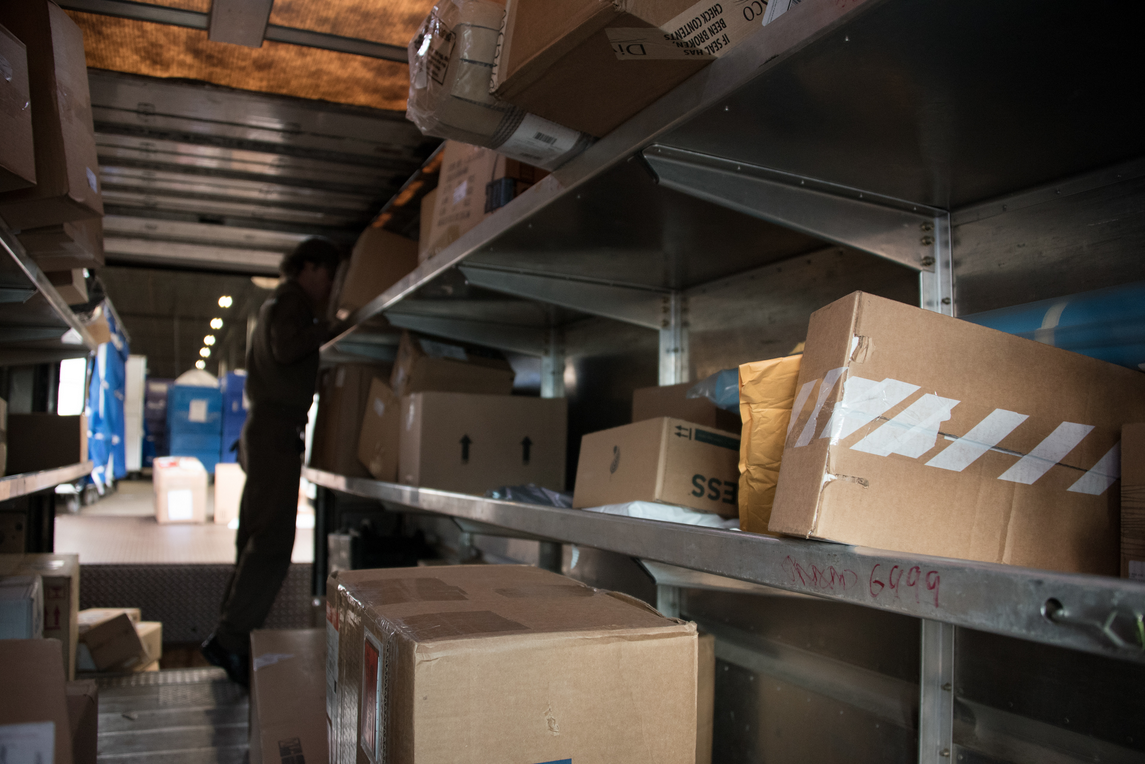
The next stop is another commercial customer. John parks in front of the truck bay and opens the back door. He spends some more time looking for yet another missing package. The time spend looking for packages boggles me; there must be something we can to about this… (to be continued)
11:19. John swings his DIAD out one more time to check which stop to go to next. Although the van is emptying fast, the rate at which it empties is diminishing: each stop seems to be less packages dense, but the time spent searching for these packages has also drastically reduced – I now understand why John was trying to get rid of as many packages as possible.
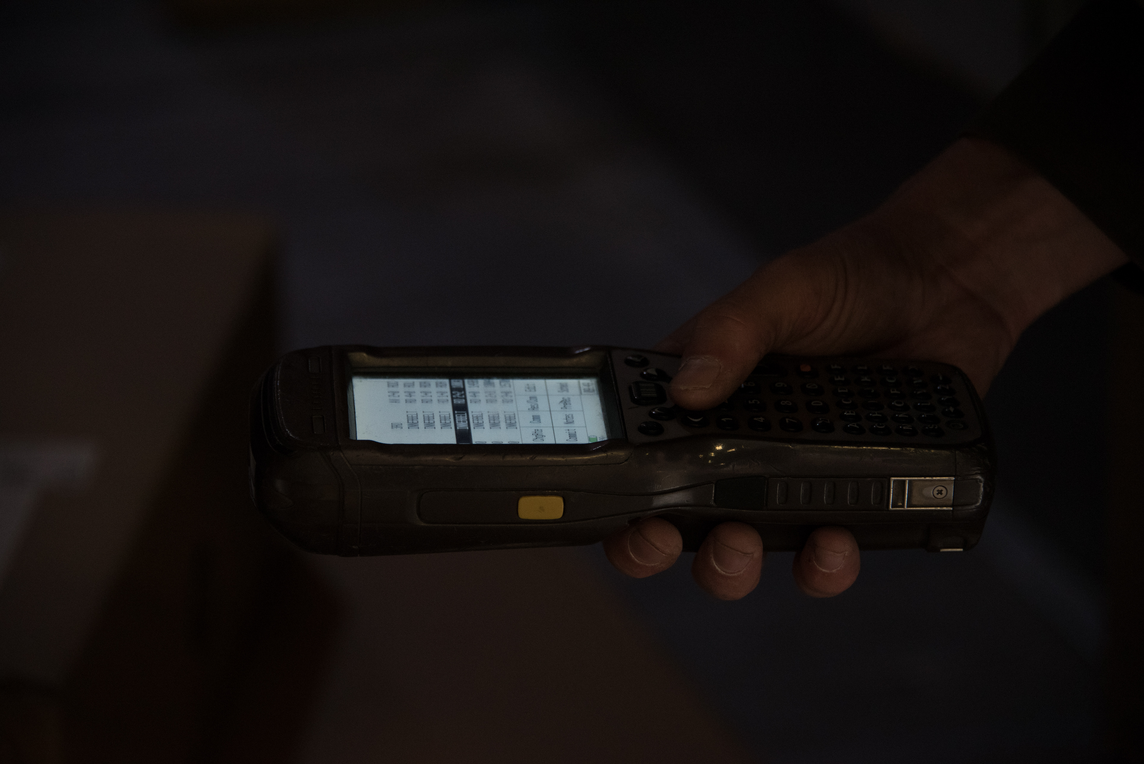
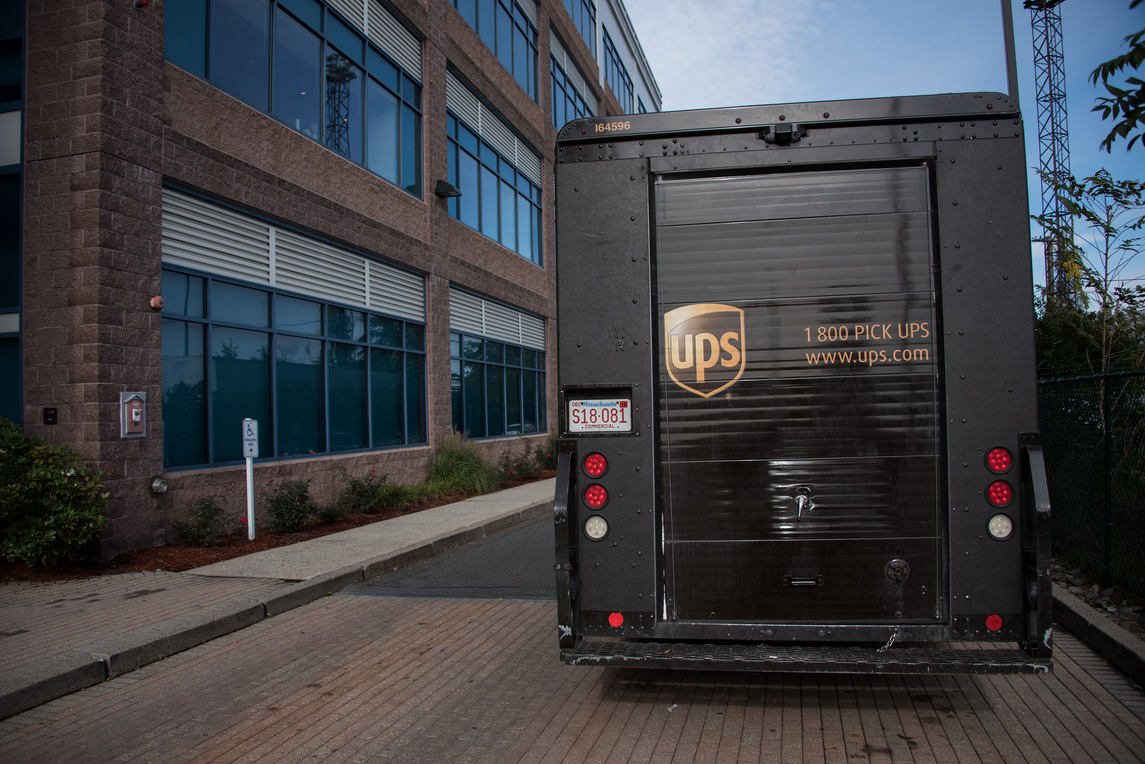
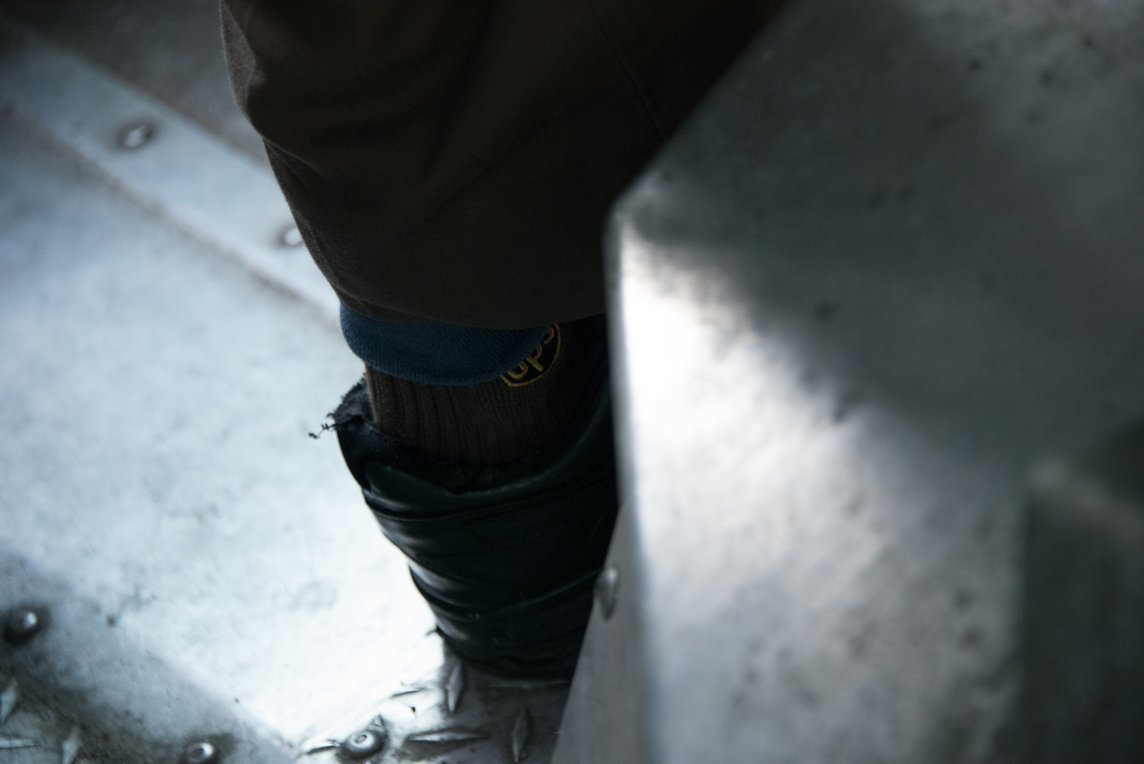
11:43. As we drive off after a residential stop, I notice that John has the UPS uniform down to the socks. “If there is anything you could change relating to your job and the way UPS operates today, what would it be?” I ask him. After a few moments of silence he answered: “I don’t know, I have not been here long enough to really know.” The answer surprises me, maybe it is because I am in the truck, but maybe John really does not mind the job. It does come with its share of relative freedom that stems from choosing the way the stops will be served during the day, it allows him to care for his two young boys and to be back home relatively early for family time, and most people have expressed a certain gratitude toward him today.
Most of the customers served today have been extremely cordial, some even wanting a chat. One seemed to remember John from a previous day and asks him how everything is doing. There is something very human about this job. It does not merely consist of bringing goods from one place to another. It involves knowing where the customers want the truck parked, who to ask for at the front desk, and building a trustful relationship with the customers. It seems, then, that although efficiency in the urban last mile effort can be improved in a variety of way, automation may spare urban drivers for another bit.
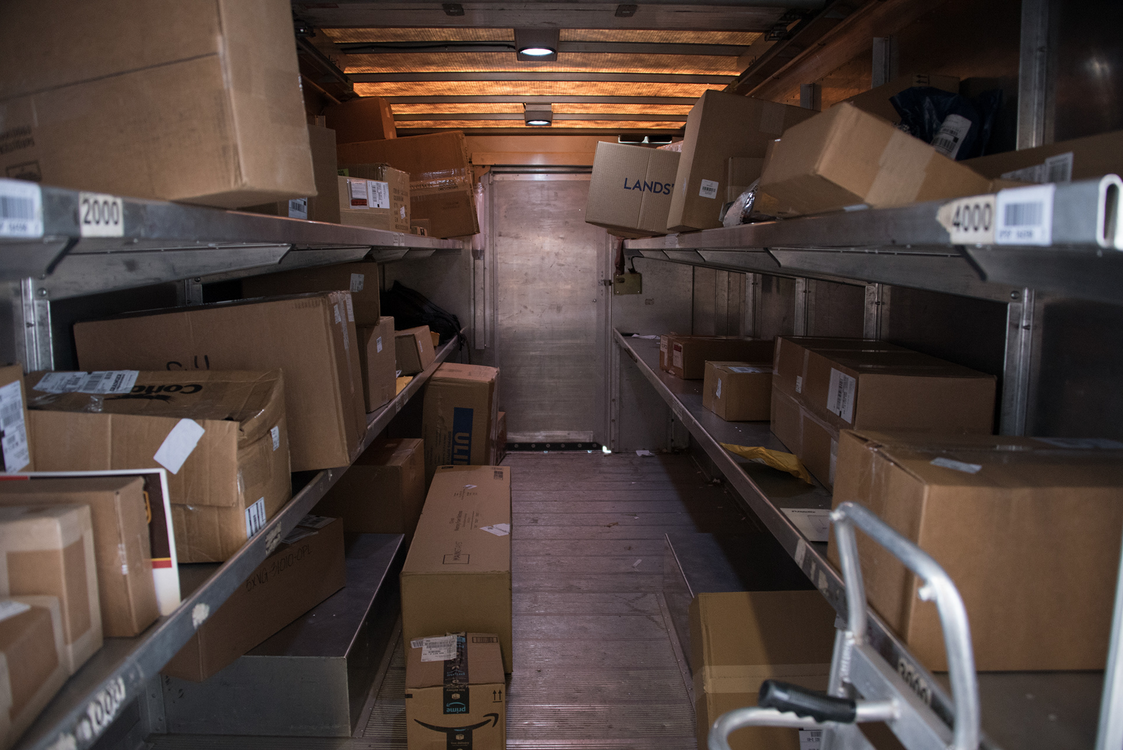
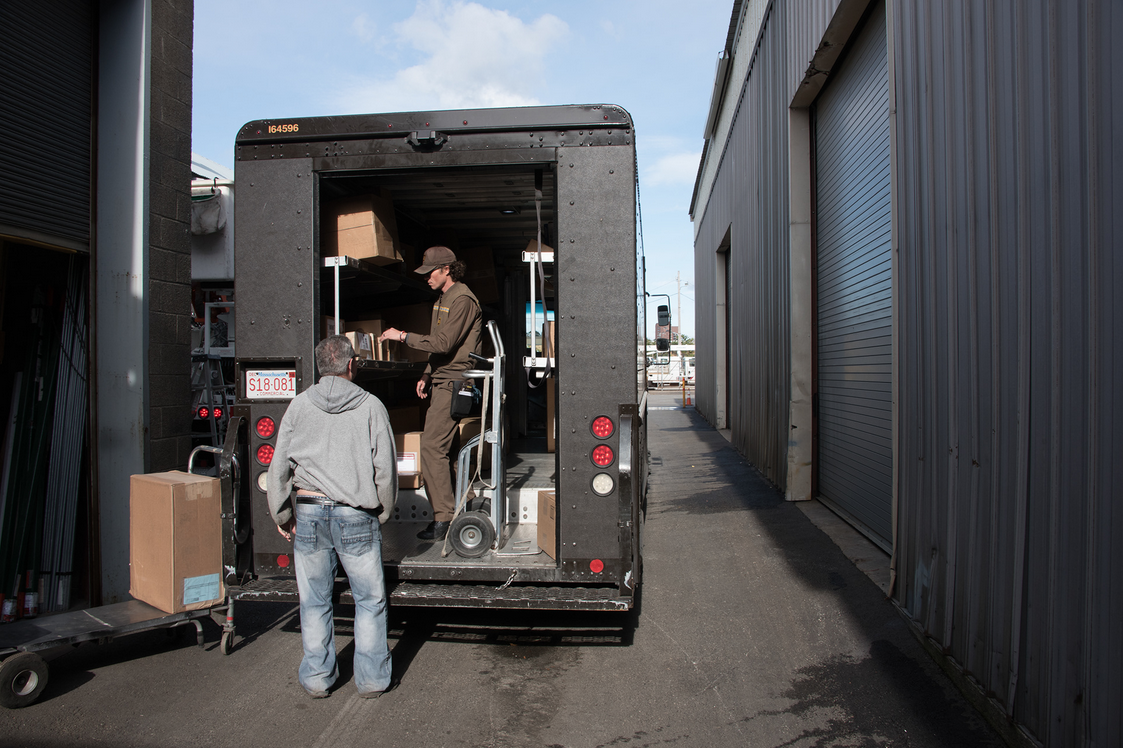
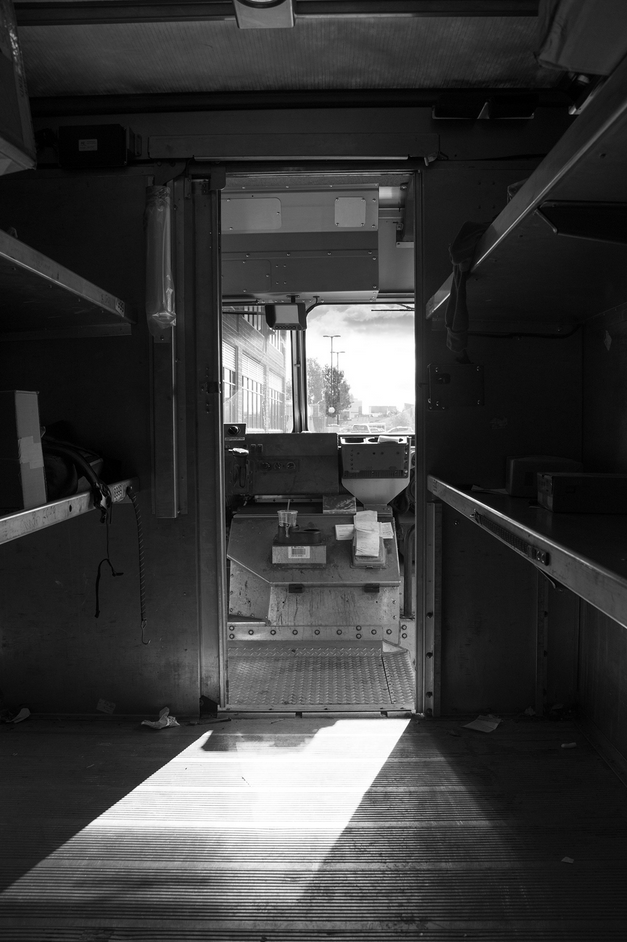
Hopefully, we will find ways to make the last mile increasingly cost-effective and energy-efficient: from packing the vans in a smarter way to routing the vans in a more efficient manner, we have the tools to make the last mile cheaper and more sustainable.
Yet, although the technology has the potential to revolutionize the industry, consumers are and will continue to be the ones driving change. If we continue to mandate shorter delivery times, delivery times will continue to decrease. All else being equal, this will increase the number of vehicles on our streets. Similarly, when ordering multiple products online, few of us (myself included) choose to consolidate our package and receive all our products ordered once a month, say. Instead, we press the option whose convenience-to-cost ratio is the highest (often the free 2-day delivery) and a single order may arrive in many packages. This not only increases vehicle miles traveled (VMT) but also fills our landfills with cardboard and other packaging waste.
It is on us, as customers, to reduce our insatiable appetite for faster access to consumer goods, it is on us to realize that choosing for a consolidated shipment once a month instead of 2-day shipping every time we make a purchase will make our urban environment friendlier and better suited for our lifestyles and will reduce energy consumption.
Obviously, the working to improve the last mile is not the only answer to the alarming state of the planet, yet it certainly is a non-negligible part of the equation.
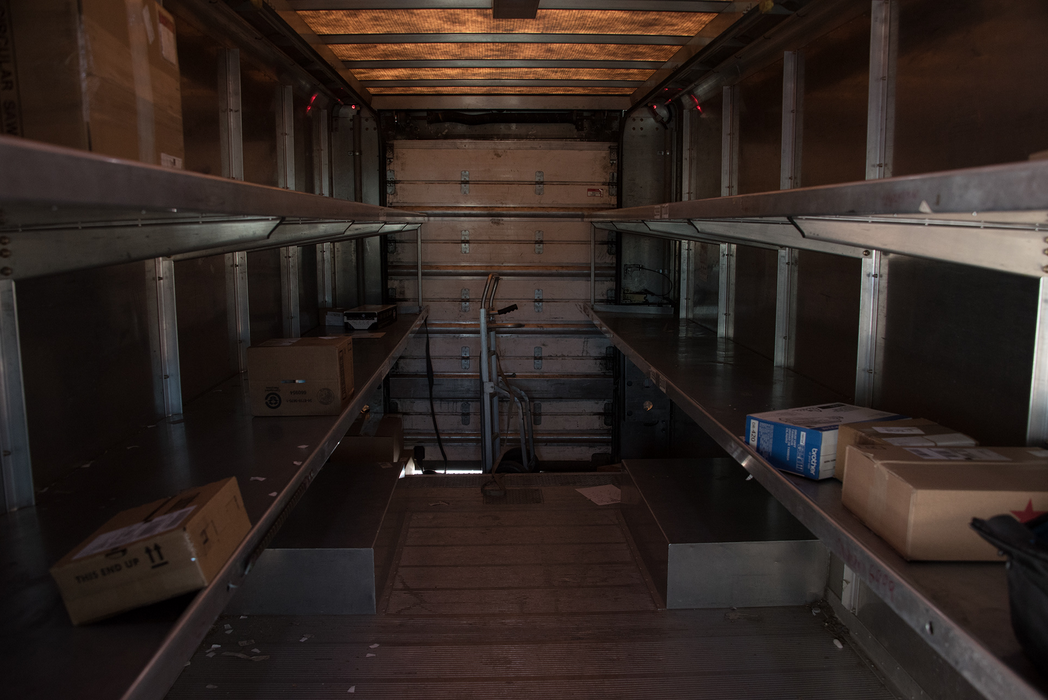
It is 12:37 when we drive back into the Somerville facility. Except for a few outbound packages that John picked-up throughout the morning the package car is now empty. John will fill it up and hit the road a second time.
Tomorrow, John will be back, his package car full once more.